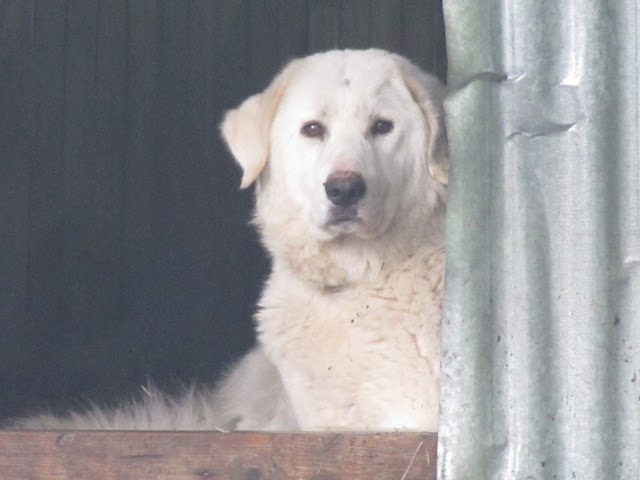 |
Pretty Tella |
Has it been a week? Good grief - I just looked up and my taxes are almost late. The barren, leafless landscape has changed nearly overnight. The farm has burst into verdant leaf and bloom, and the grass has had to be mowed twice!
March was such a whirlwind, I've let some important things sneak up on me. But we had a blast the past few weeks with a bunch of significant farm happenings:
DFW Fiber Fest, the
Wildflower Fiber Retreat, and the shearings of both
alpacas and
sheep. I've been living with the fleeces filling up my living room and utility room, and am just itching to get into those bags up to my elbows.
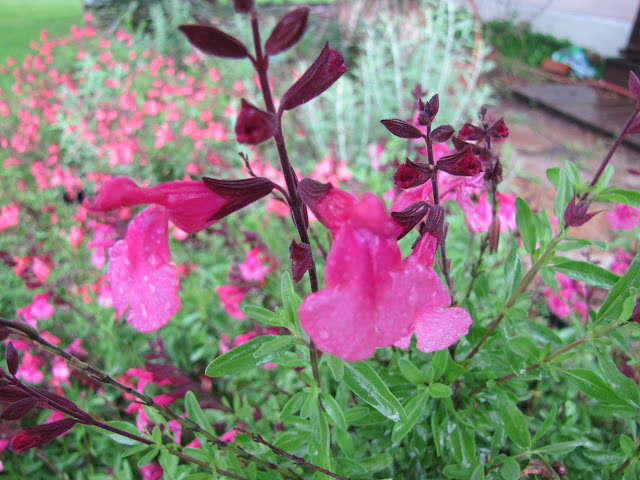 |
Salvia Greggii |
But first, we continue getting the colored fiber cleaned up for our unbelievably patient 2011 shareholders who each deserve medals. Today, I tumbled gray alpaca fiber until I nearly turned blue, but the softness and overall cleanliness of the fiber kept me on Cloud Nine the whole time.
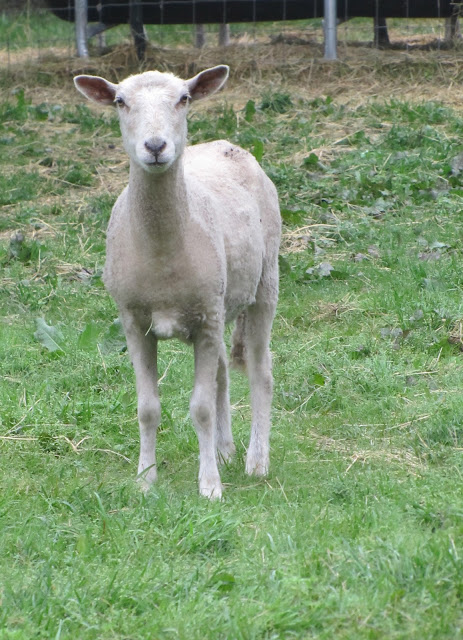 |
Sweet Rachael |
This coming Saturday, we'll host another wonderful
Tri-Loom class in the LRB. Since we have to keep the classes small, I know we'll have another class on the calendar soon. If you've been wanting to add this
easy-peasy weaving technique to your list of skills, let me know, and you'll be the first on the list to make up our next class. It's more than just triangles - our friend Midge Jackson has designed some darling vests and other clever garments with these woven pieces. I'll have the patterns available at the Little Red Barn.
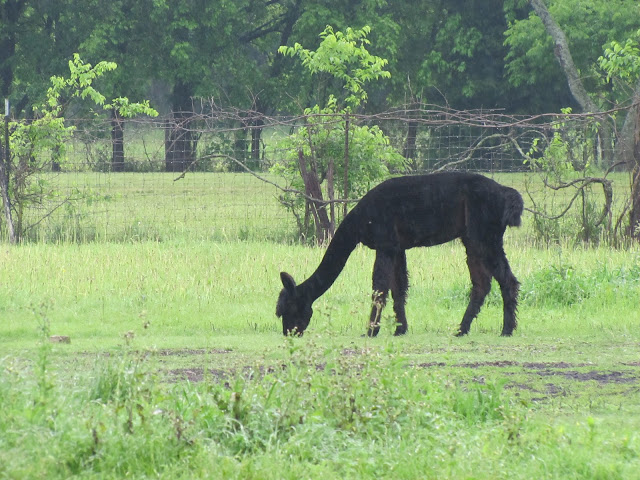 |
Fleeceless Solomon |
This month I will finally get to attend the regular Third and Fourth Saturdays' Spin/Knit-ins at the LRB (on the 21st and 28th)! Seems like forever! We've had several new folks join the group and I can't wait to meet you in person!
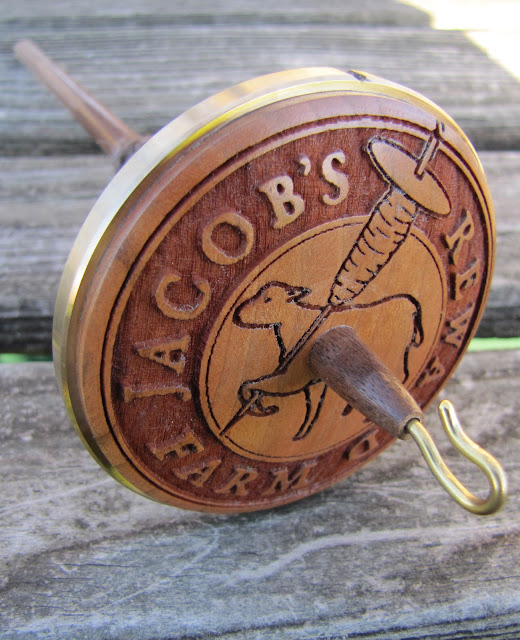 |
The Golding |
If you have your name on the list for one of the next batch of Golding spindles, hang in there. We almost have enough folks poised to send in our order. Remember this time we can order either the 2.5" spindle or the smaller, lighter 2" spindle. There's still time to get on the list if you'd like.
Email me for details. Farm Women School is still moving forward, behind the scenes, and will continue to develop over the summer. We hope to unveil the curriculum just before the end of the year, for enrollment in January.
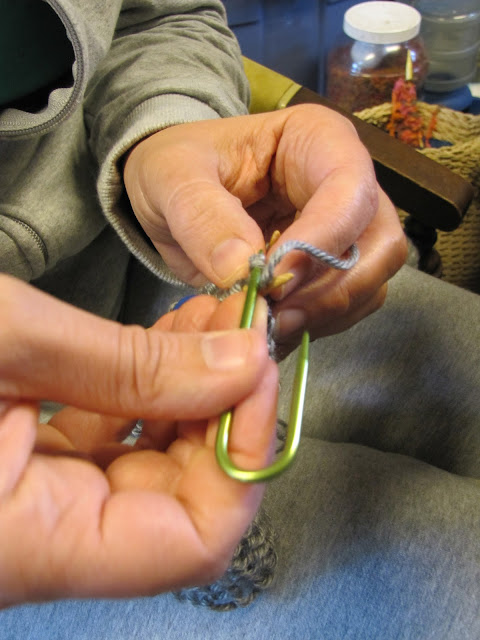 |
Knitting Student Tackles Cables |
As we move into the warmer months, the hectic pace slows a bit here at the farm. Oh sure, there's
Farm Camp during the last weeks of June, and Emma and I will be off to the
Maryland Sheep and Wool Festival over the first weekend in May, but all in all, we're getting to the "slow" time in the fiber year. Just right for all the catching up I'm needing to do.
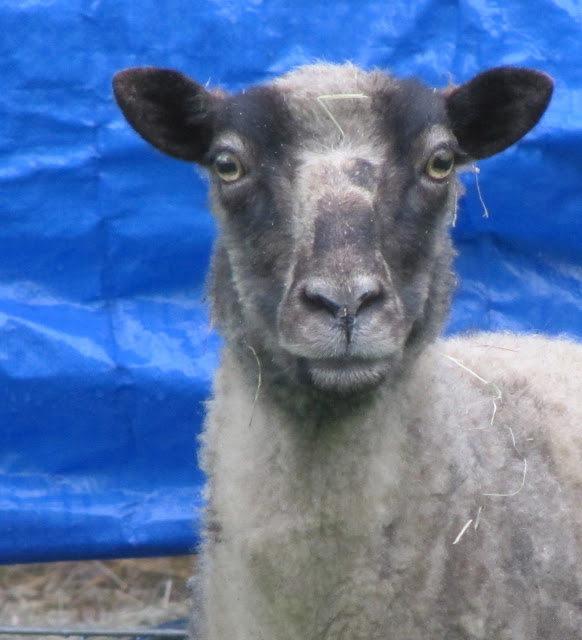 |
Nutty Phoebe |
As you know, none of this gets done by me alone - I have a wonderful crew of Help Shareholders, a strapping high school fellow who loves to work outside with his hands, a Little Red Barn full of knitting and spinning pals, and you, precious friend, who hang out with me here in Blogland. I love your company and your encouragement.
 |
Wet Hens |
On a personal note, you may know that my only child, Emma, has been away in Hawaii homeschooling with my sister and her family for the past six months. I'm delighted to report that she's back home now and we're enjoying having her back something fierce. We're up to our necks planning for her future and what that might look like. Focusing on Emma now may necessitate a few adjustments around the farm, but I'll share those things as they develop.
 |
April Showers |
In the meantime, know that our day-to-day life here on the farm continues in its steady rhythm and routine, punctuated by fun events and the laughter of friends. You bless us!
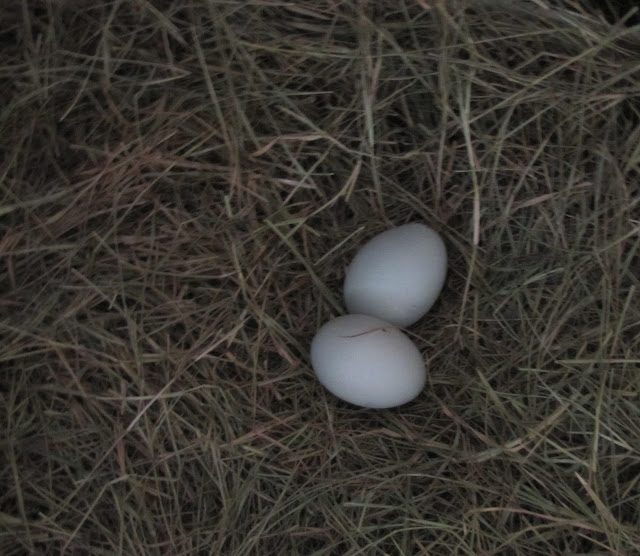 |
Easter Eggs |